This example comprises a single hexahedral element (1m x 1m x 1m) subjected to uniaxial displacement. The element contains a single fracture orientated in the horizontal plane with the properties listed below. The fracture spacing corresponds to the height of the element so there is a single fracture in the element.
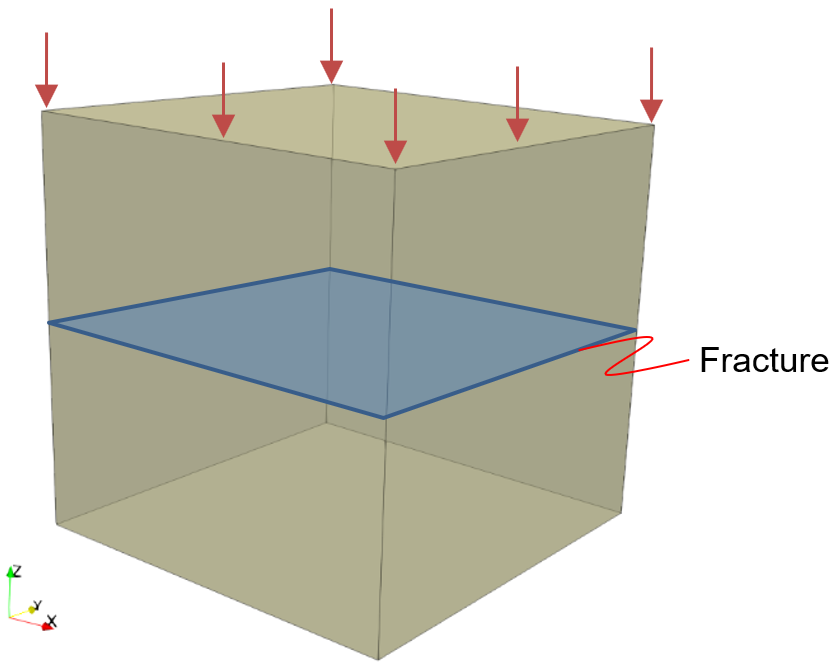
|
Fig. 1 Prescribed loading on element with embedded continuum fracture
|
Material Properties
The properties used in this simulation are listed below.
Property
|
Value
|
Young's Modulus
|
2000 MPa
|
Poisson's Ratio
|
0.20
|
Porosity
|
0.35
|
|
The additional material parameters related to the embedded fractures are:
Contact Surface Properties
|
Value
|
Normal stiffness
|
1000 MPa
|
Initial aperture
|
0.01m
|
Initial porosity
|
0.01
|
Maximum joint stiffness
|
30000 MPa
|
Spacing
|
1.0 m
|
|
The data file for the example is in: Fract_003\Data\fract_003_case01.dat. The basic data includes:
1Material_data defines the material properties of the model, including the fracture set associated with the embedded fracture. 2Fracture_data assigns the properties of embedded fracture as well as the fracture spacing and local coordinate system. 3Global_loads prescribes axial displacement on the element top surface. 4History_point outputs displacement, stress values, and fracture state variables at every 0.01s.
Note that only key data structures are described below.
|
Material_data defines the material properties of the model, including the fracture set associated with the embedded fracture.
Data File
|
|
*Material_data NUM=1
Material_name "Sample"
Units IDM=4
"MPa"
"m"
"s"
"Celsius"
Grain_stiffness 3.0000E+10
Grain_density 2710.00
Porosity_model_type 1
Porosity 0.35000
Elastic_model_type 1
Isotropic_elastic_properties IDM=2
2000
0.20000
Fracture_set_names IDM=1
"fract_set1"
|
1Material name, units and grain stiffness are defined as listed. 2Density is defined as 2710 kg/m3. 3Constant porosity type model is used. The value is defined as 0.35. 4Young’s modulus and Poisson’s ratio are defined as 2000MPa and 0.2, respectively. 5The material data structure is associated with “fract_set1” fracture set.
|
|
Fracture_data assigns the properties of the embedded fracture as well as the fracture spacing and local coordinate system.
Data File
|
|
* Fracture_data NUM=1
Name "fract_set1"
Units IDM=4
"MPa"
"m"
"s"
"Celsius"
Propagation_model_name "PreExist"
Fracture_spacing 1.00
Coordinate_system_name "Fracture_Set1"
Normal_stiffness_model "Bandis"
Normal_stiffness_properties IDM=3
1000
0.01
300000
Normal_strength_model "Elastic"
|
1Fracture data name and units are defined as listed. 2The propagation model type is defined as “PreExist”, indicating the embedded fracture as a pre-existing entity. 3Fracture spacing is defined as 1.0m. 4The fracture data is associated with coordinate system named “Fracture_Set1”. 5The fracture normal stiffness model is defined as Bandis model. 6The input values for Bandis model are defined, including joint stiffness, initial aperture and maximum joint stiffness. 7Elastic normal strength model is defined, indicating no formal failure criterion is applied. |
|
Global_loads prescribes axial displacement on the element top surface.
Data File
|
|
* Global_loads NUM=1
Prescribed_displacement IDM=3 JDM=1
0.0 0.0 -0.025
Pres_displacement_geom_set IDM=1
"Top"
Pres_displacement_geom_ass IDM=1
1
|
1Geometry set “Top” is prescribed with downward axial displacement of 0.025m. |
|
History_point outputs displacement, stress values, and fracture state variables at every 0.01s.
Data File
|
|
* History_point NUM=1
Name "Set1"
Group 1
Output_frequency_time 0.01
Point_coordinates IDM=3 JDM=1
1.0 1.0 1.0
Displacements IDM=1
"DISP_Z"
Stresses IDM=3
"STRS_XX" "STRS_YY" "STRS_ZZ"
Fracture_state_variables NUM=2
"F_kn" "F_dispn"
|
1The History_point data structure is associated with Group 1. 2The history data is output at an interval of 0.01s throughout the simulation time. 3The history data is monitored at coordinate point (1,1,1). 4Displacement, stresses and fracture state variables as listed are output at the monitored history point. |
|
The result files for this example is available in directory: fract_003\Results. The tangent modulus of the jointed element is expected and observed in Figure 2 to be lower than the intact counterpart in the fracture closure stage due to higher fracture compliance. Figure 2 also shows that as the joint gradually closes, the tangent modulus progressively increases to the value similar to the intact counterpart. This indicates the onset of intact compression. Figure 3 exhibits sublinear increase of joint displacement, which is a manifestation of supralinear increase of fracture stiffness as shown in Figure 4. This can be explained by the inverse relationship between joint displacement and fracture stiffness, provided that the prescribed load is constant. Figure 5 shows that the porosity is reduced from 0.01 to 0.002, which corresponds to about 80% reduction due to joint normal displacement.
Geometry Set
|
Fluid Volume (m3)
|
Fluid Volume Flow Rate (m3/Ma)
|
west
|
244.439
|
488.878
|
east
|
295.113
|
590.226
|
|
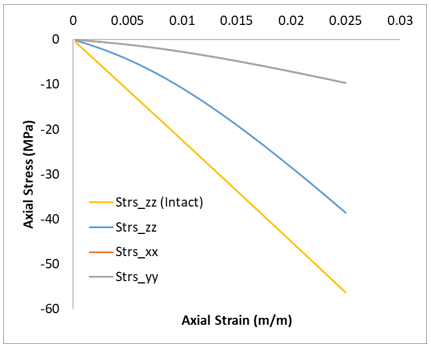
|
Fig. 2 Comparison of axial stress with intact sample
|
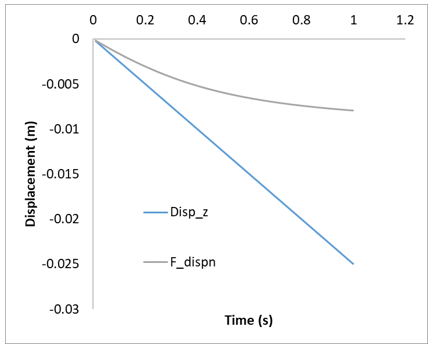
|
Fig. 3 Comparison of axial and fracture displacement
|
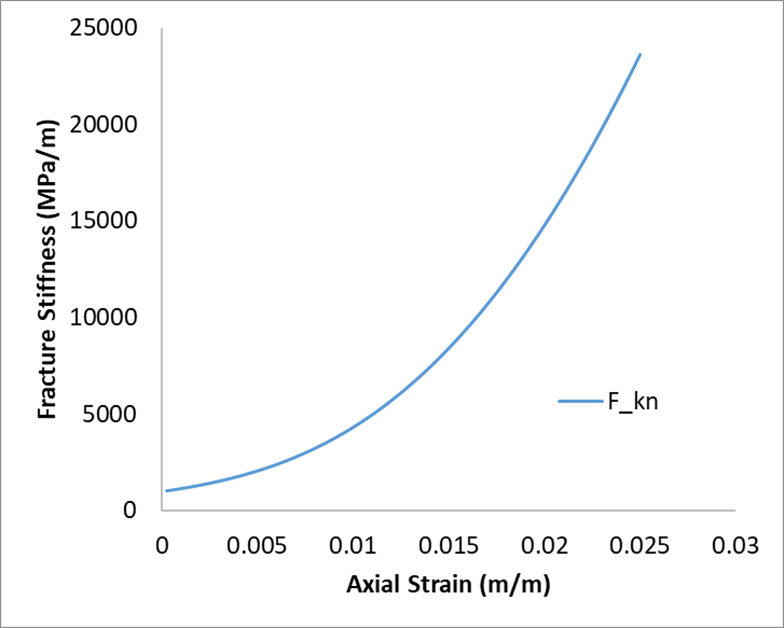
|
Fig. 4 Supralinear increase of fracture stiffness
|
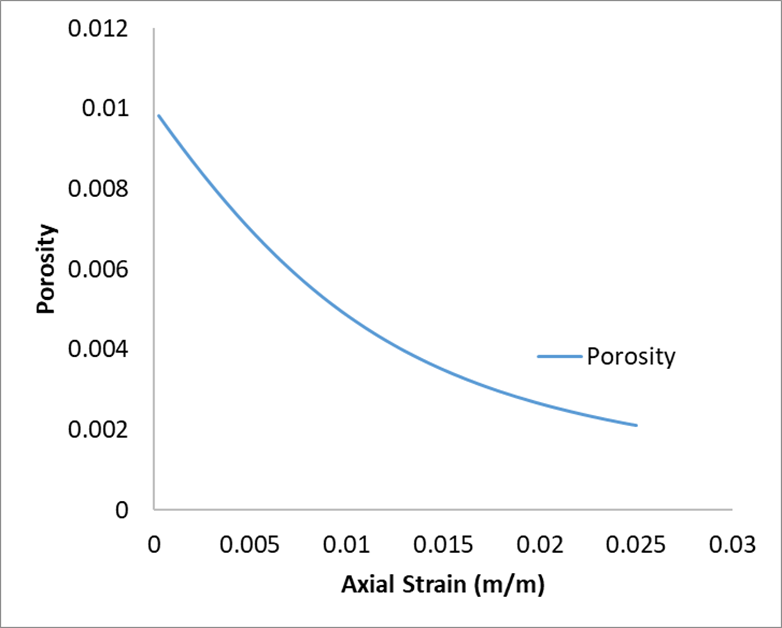
|
Fig. 5 Reduction of porosity due to joint closure
|
|